製品組立製品組立はセル生産方式を取り入れており、「多品種少量生産」や「お客様の生産変動対応」が可能です。
また、バーコード管理システムにより「誰が」「いつ」「何を」組立、検査したかが、瞬時にトレースでき生産状況も随時把握可能です。 |
 |
 |
 |
 |
|
 |
※ 帽子の色 :(黄色)工程内検査員 / (ピンク)出荷検査員 |
 |
|
 |
|
 |
 
製品組立では、「セル生産方式」を導入しており、多品種少量生産での対応ができます。

・ ATM 鑑別UNIT
・ ATM ソータUNIT
・ バーコードプリンタ
・ 監視カメラ UNIT など |
 |
|
|
|
 |
|
 |
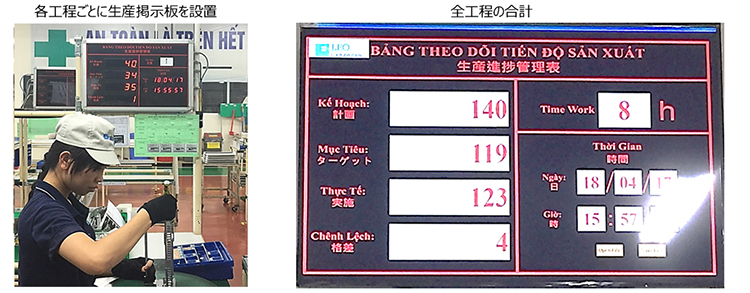
生産状況を随時把握できるよう各組立ラインに生産進捗版を設置しています。
各組立ラインの1時間ごとの「目標台数」を設置し目標値に達しない場合は、現場監督者が状況を確認し、対応策を検討します。
※ プレス工程も同様に「生産掲示板」を設置し進捗管理を行っています。 |
 |
|
 |
|
 |
※帽子の色 :(黄色)工程内検査(PQC) / (ピンク)受入・出荷検査(I/OQC) / (青色)現場監督者
【検査頻度】
工程内検査(PQC) :各工程ごとに3pcs/Hで抜取検査を行い保証
出荷検査(OQC) : AQL(抜取基準)に基づき抜取検査
【日常管理】
バリ高さ管理 :XY管理図により各工程のバリ高さを管理。それにより、随時金型状態を把握し金型メンテナンススケジュールと併用し金型管理を行って います。
測定工具管理 :測定器の内・外部校正はもちろん、使用頻度の高いPINゲージなどはXY管理図により定期管理。 |
 |
|
 |
|
 |
作業者の職業に必要な技能と地位の向上、及び作業品質安定化のため、重要管理ポイントである作業に於いては、作業認定制度を設け特定の教育を受講し「試験」に合格した者のみが作業に従事しています。
◆ 作業認定工程
① 金型段取作業
② タレットパンチ/レーザ加工
③ プレスブレーキ
④ 各種溶接作業
⑤ スピンカシメ
⑥ 各種測定機(二次元、三次元、Rohs測定) など
|
 |
|
|
|
|
|
 |
|
 |
レオ電子では2005年より使用する原材料・部品の調達にあたり環境に影響を及ぼす化学物質を調査し環境負荷の少ないものを優先的に採用しています。
また、レオ環境マネジメントシステム(LCMS:LEO Chemical-Substances Management System)を設定し外注先様の理解とご協力を得ながらグローバルにグリーン調達を実施しております。
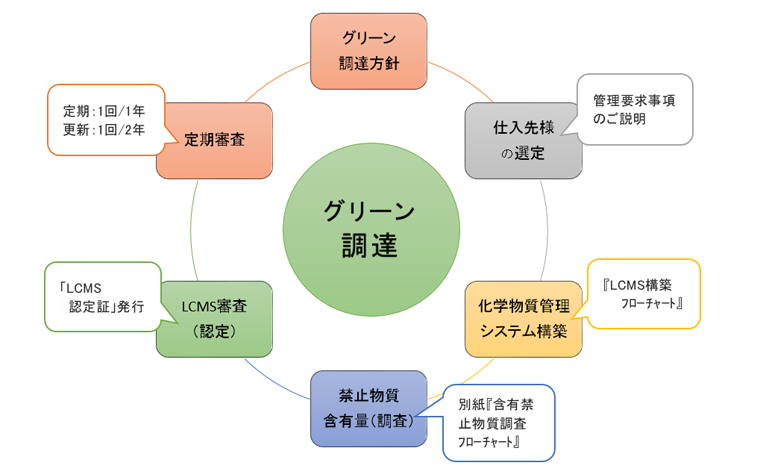 |
 |
|
|